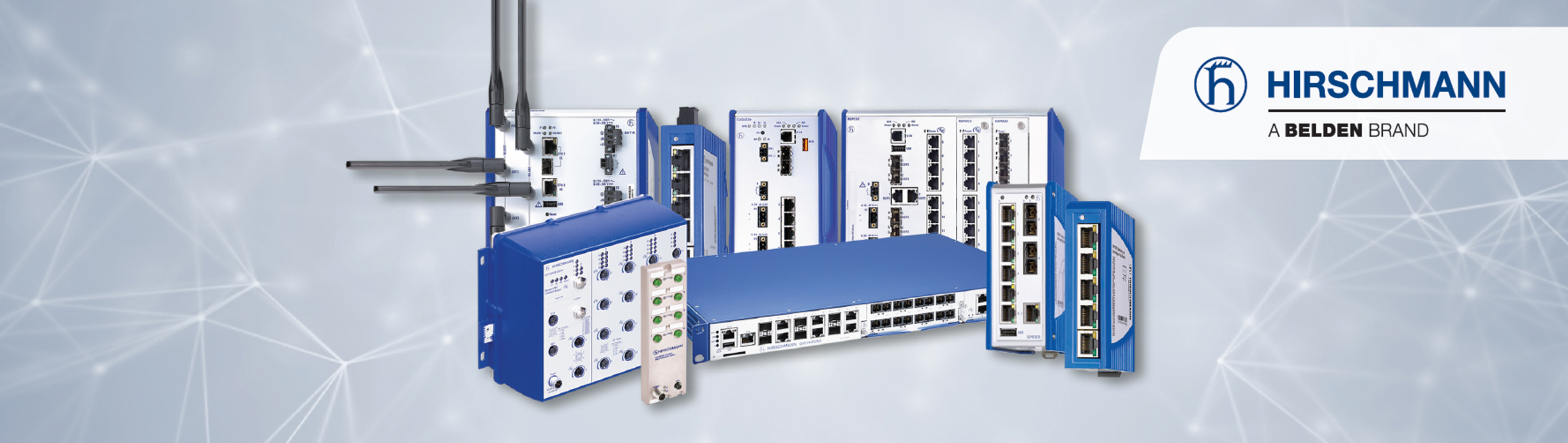
Introduction
As different applications and networks converge in industrial environments, it is no longer enough to master the basic functionality of these networks. To keep pace with the growing size and performance requirements of IP networks, today the network administrator requires extensive technical and practical knowledge about various unicast and multicast routing mechanisms.
Objective
This course builds on the experience gained from “Industrial Networking (CT2)” providing network experts with intensive theoretical and practical knowledge about unicast and multicast routing. A special emphasis is placed on deploying routing protocols in complex industrial environments. This enables the participants to provide comprehensive support, both for demanding projects and their daily work.
Intended Audience
Technology training course for System Engineers, Network Designers and Support Technicians who are building, supporting or migrating an Industrial Ethernet network.
Prerequisites
Participant’s Background: Basic knowledge is required, for example previous attendance of the “Industrial Networking (CT2)” course. The participant should bring a laptop with Ethernet connection. Administrator rights are required.
Course Condition:
The cost of this course is $1,199ex per person. There is a minimum participant requirement for the course to proceed. Full payment is required prior to course commencement. Cancellation fees of 20% will apply if less than 48 hour notice is given.
Modules
Routing
- Routers and their functionality
- IP addressing
Unicast Routing Protocols
Router Redundancy
Multicast Routing Protocols
Schedule
2 days
9.00am to 4.30pm (approx.)
Lunch and light refreshments will be provided.
Course OutlineBook Now |