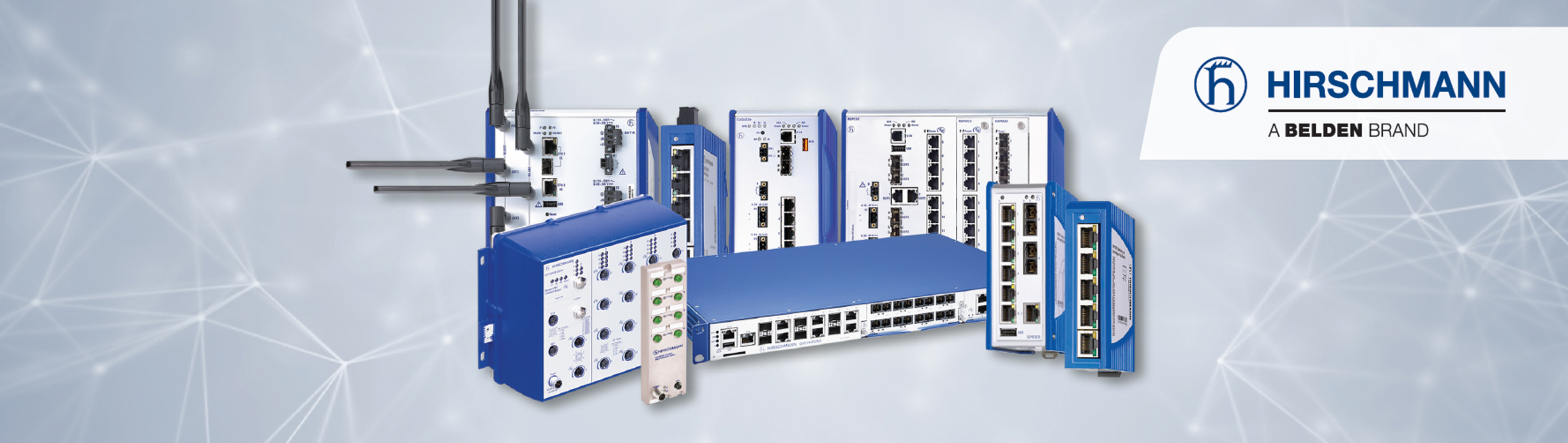
Introduction
HiOS is an entirely new operating system for Industrial Ethernet, combining high performance with robust security. It permits the use of intelligent infrastructure in time-critical applications that were previously a ‘hard-wired’ domain via new point-to-point connection technology.
With zero switchover time, the PRP (Parallel Redundancy Protocol) and HSR (High-Availability Seamless Redundancy) redundancy methods ensure smooth production processes. Comprehensive security mechanisms protect networks against attacks and operating errors.
Objective
In a professional environment the participants receive in-depth knowledge about the Hirschmann Operating System (HiOS) Layer 2 functionality of the various RSP variants, MSP, GREYHOUND, and EES devices. This includes installation, commissioning, and supervision.
Intended Audience
Product training course for System Engineers, Network Designers and Support Technicians.
Prerequisites
Participant’s Background: An understanding of Ethernet and TCP/IP, for example “Industrial Ethernet (Ct1)” and “Industrial Networking (CT2)” is required. The participant should bring a laptop with Ethernet connection. Administrator rights are required.
Course Condition:
The cost of this course is $1,299ex per person. There is a minimum participant requirement for the course to proceed. Full payment is required prior to course commencement. Cancellation fees of 20% will apply if less than 48 hour notice is given.
Modules
Basic Settings
- Software Management
- Configuration Management
- External Memory
Switching
- Port Configuration
- Rate Limiter
- IGMP
- VLANS
- Quality of Service
Redundancy
- MRP
- PRP
- HSR
- Rapid Spanning Tree
- Subring
- Link Aggregation
- MRP over LAG
- Linkbackup Network
Network Security
- Port Security
- Denial of Service (DoS)
- Authentication (802.1x)
- Access Control Lists (ACLs)
Diagnostics
- Port Mirroring
- Device Status
- Security Status
- Topology Discovery
- Configuration Check
- Event Log
- Persistent Logging
- SFlow
Advanced
Schedule
3 days
9.00am to 4.30pm (approx.)
Lunch and light refreshments will be provided.
Course Outline Book Now |