Our customer is one of the largest private optical and ophthalmic research centres in the world. They design, manufactures, and market lenses to correct or protect eyesight. Their aim is to design and craft lenses that bring the best in vision and eye protection to all, in order to preserve everyone’s eye health.
Energy is vitally important for the business, not only is it their second highest operating expense, but our customer sees it as an opportunity to drive growth within their business by monitoring their consumption to identify how much electricity is been used by every machine.
Goals and needs
With a reputation built on robustness and reliability, our customer relies on critical power infrastructure to exceed its customer expectations.
By integrating smart technology within their research centre infrastructure, they can develop an unparalleled understanding of their site, machines, and processes. This new connectivity combined with a universal view of operating parameters will enable a reduction in energy consumption, costs and emissions and make the deployment of resources more efficient.
To create more efficient research centre, they will need to develop a deep understanding about the way they use energy and resources. By accurately measuring and centrally monitoring energy consumption, it will be possible to improve efficiency across their research centre. Of vital importance, is the need to track the status of key operating parameters in real time in order to immediately address virtual and physical anomalies, in turn resulting in maximum uptime and reduced operating expenditure.
With energy prices on the rise, and floor space at premium, power density and the optimisation of infrastructure is under the spotlight. Optimising their performance will significantly impact the bottom line and improve the facility’s overall energy usage.
By increasing the performance of infrastructure, organisations are able to reduce energy consumption, aligning operational efficiency with environmental responsibility. This dual benefit supports long-term sustainability goals while addressing immediate economic challenges, making energy management strategies a critical step toward a more sustainable and cost-effective future.
The Solution
One such system – designed to meet these demands is Optimise, IPD’s energy management solution, which will enable the research centre managers to make fully informed decisions.
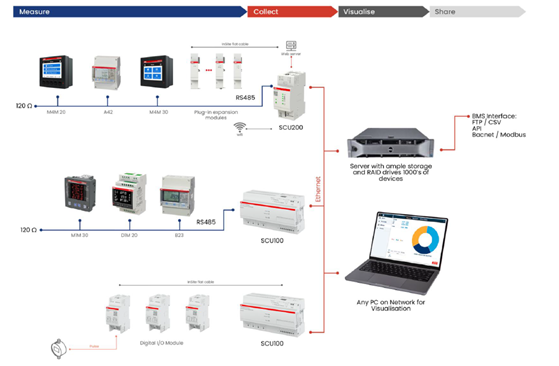
Optimise is a fully integrated solution, that includes metering hardware and energy management software. The advantages of the Optimise solution is that it has an open protocol (Modbus or Bacnet), and easy to use web browser interface, rich visual display, role-based user access, user friendly navigation, automated reports, custom displays, energy dashboards and data backup. This system allows users to monitor electricity, gas, water, thermal, diesel and waste.
In addition, a modular power distribution system is a key element in implementing a power monitoring solution within a research centre. This advanced – yet simple to use – system enables research centre managers to manage power usage more effectively and rapidly respond to changing power requirements.
To learn more about how IPD Optimise can help you meet your energy management needs, contact us today. |