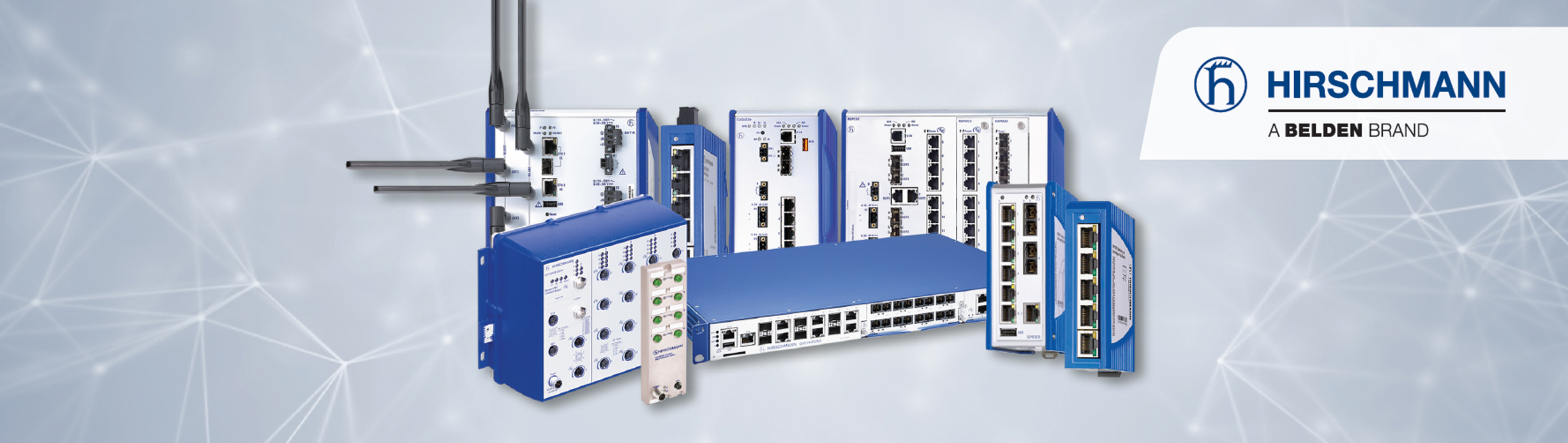
Introduction
Today all manufacturers consider Ethernet essential as a future-proof protocol for communication between various hardware and software platforms - both inside and outside industrial environments. Ethernet makes it possible to connect many different PLCs and PC-based systems, in a seamless transparent network, which stretches from the factory floor to the boardroom.
Objective
In this Industrial Ethernet course the participants will learn details of the technical fundamentals and deployment objectives of the world’s most widely used LAN communication protocol. At the end of the course the participants will have a good understanding of Ethernet, as well as its role in industrial networking, both now and into the future.
Intended Audience
Technology training course for System Engineers, Network Designers and Support Technicians who are building, supporting or migrating an Industrial Ethernet network.
Prerequisites
Participant’s Background: No previous knowledge of the subject is required. The participant should bring a laptop with Ethernet connection. Administrator rights are required.
Course Condition:
The cost of this course is $1,199ex per person. There is a minimum participant requirement for the course to proceed. Full payment is required prior to course commencement. Cancellation fees of 20% will apply if less than 48 hour notice is given.
Modules
Standardised Bodies
- ISO/OSI Layer Model
- IEEE 802
- IETF
- EC
The Physics of Ethernet
- Copper-based Networks
- Fiber-based Networks
- Physical Interfaces
- Bandwidth/Speed
- Half Duplex and Full Duplex
- Ethernet Frame
- Understanding MAC addresses
Ethernet in Half Duplex Mode
- Ethernet access method: CMSA/CD
- Hubs
Ethernet in Full Duplex Mode
- Autonegotiation
- Switches
- Switching Mechanisms
- Forwarding Databases
- Delay of frames
Network Availability
- Topologies
- Rapid Spanning Tree
- Link Aggregation
- Industrial Redundancies (MRP, PRP, HSR)
Traffic Control
- Flow control
- VLANs
- Quality of Service
Schedule
2 days
9.00am to 4.30pm (approx.)
Lunch and light refreshments will be provided.
Course Outline Book Now |